Пыж ДВП осаленный 200шт, все калибры
Интернет-магазин: В наличии
Новосибирск, пр-т Строителей, 19: В наличии
Новосибирск, ул. Нарымская, 23: В наличии
Новосибирск, ул. Мичурина, 12: В наличии
Бердск, ул. Карла Маркса, 1: В наличии
Искитим, ул. Станционная, 1б (ЖУМ): В наличии
Черепаново, ул. Республиканская, 61: В наличии
Барнаул, ул. Взлетная, 2к: Нет в наличии
Бийск, ул. Больничный взвоз, 8: В наличии
Майма, ул. Подгорная, 37: В наличии
Куйбышев, ул. Чехова, 18: В наличии
Купино, ул. Максима Горького, 4: В наличии
Интернет-магазин: Нет в наличии
Новосибирск, пр-т Строителей, 19: В наличии
Новосибирск, ул. Нарымская, 23: В наличии
Новосибирск, ул. Мичурина, 12: В наличии
Бердск, ул. Карла Маркса, 1: В наличии
Искитим, ул. Станционная, 1б (ЖУМ): Нет в наличии
Черепаново, ул. Республиканская, 61: В наличии
Барнаул, ул. Взлетная, 2к: Нет в наличии
Бийск, ул. Больничный взвоз, 8: Нет в наличии
Майма, ул. Подгорная, 37: Нет в наличии
Куйбышев, ул. Чехова, 18: В наличии
Купино, ул. Максима Горького, 4: В наличии
Интернет-магазин: В наличии
Новосибирск, пр-т Строителей, 19: В наличии
Новосибирск, ул. Нарымская, 23: В наличии
Новосибирск, ул. Мичурина, 12: В наличии
Бердск, ул. Карла Маркса, 1: В наличии
Искитим, ул. Станционная, 1б (ЖУМ): В наличии
Черепаново, ул. Республиканская, 61: В наличии
Барнаул, ул. Взлетная, 2к: В наличии
Бийск, ул. Больничный взвоз, 8: В наличии
Майма, ул. Подгорная, 37: В наличии
Куйбышев, ул. Чехова, 18: В наличии
Купино, ул. Максима Горького, 4: В наличии
Интернет-магазин: В наличии
Новосибирск, пр-т Строителей, 19: В наличии
Новосибирск, ул. Нарымская, 23: В наличии
Новосибирск, ул. Мичурина, 12: В наличии
Бердск, ул. Карла Маркса, 1: В наличии
Искитим, ул. Станционная, 1б (ЖУМ): В наличии
Черепаново, ул. Республиканская, 61: В наличии
Барнаул, ул. Взлетная, 2к: В наличии
Бийск, ул. Больничный взвоз, 8: В наличии
Майма, ул. Подгорная, 37: В наличии
Куйбышев, ул. Чехова, 18: В наличии
Купино, ул. Максима Горького, 4: В наличии
Пыжи ДВП, войлок | БЕЗ ПОРОХА
<Any>Арбалеты / Луки-Арбалеты—Блочные—Рекурсивные—Арбалеты-пистолеты—Bowmaster—Man Kung—Poe Lang—Прочие-Луки—Блочные—Классические—Традиционные-Стрелы / Наконечники—Стрелы для арбалета—Стрелы для лука—Наконечники—Инсерты—Оперение—Хвостовики—Экстракторы стрел-Запчасти для арбалетов-Аксессуары для арбалетов-Аксессуары для луков—Полочки—Прицелы—Краги—Релизы / Напальчники—Пип-сайты-Колчаны / Киверы / Пеналы-Инструмент-Щиты / СтрелоулавливателиСтрайкбол-Оружие по типу—Автоматы АК-серии—Автоматы М-серии—Автоматы прочие—Винтовки—Пистолеты-пулемёты—Пистолеты—Пулемёты-Оружие по производителю—Cyma—Gletcher—E&L—King Arms—LCT—WE—Прочие-Магазины / лоадеры-Шары-Газ-Очки / Маски-Аккумуляторы и ЗУ-Аксессуары-Запчасти—Внешние элементы / обвес—Gear-box—Электро компоненты—Хоп-ап—Для СО2 / green gas оружияПневматическое оружие-А+А (Атаман)-Baikal (ИМЗ)-ASG-Borner-Crosman-Cybergun-Gamo-Gletcher-Hatsan-Smersh-Stalker-Umarex-ПрочиеПули / Шарики-Пули калибра 5,5 мм-Пули калибра 6,35 мм-Квинтор-Люман-Шмель-Crosman-Gamo-Haendler & Natermann-JSB-RWS-Шарики ВВ-ПрочиеCO2 баллоныОптика-Оптические прицелы—ВОМЗ (Pilad)—Nikko Stirling—Target Optic—Leapers—Прочие-Коллиматорные прицелы-Диоптрические прицелы-Лазерные целеуказатели-Подствольные фонари-Аксессуары для оптикиКронштейны-По типу крепления—Weaver / Picatinny—Ласточкин хвост—Боковые кронштейны—Наствольные кронштейны—Планки—Другие-По производителю—ВОМЗ—ЭСТ (г.

что это такое? Расшифровка аббревиатуры материала, белые мягкие облагороженные и другие плиты. Как выглядит цветная ДВП? Плотность
Древесина в последние годы редко используется в деревообработке. Это дорогой материал, поэтому при проведении строительных и ремонтно-отделочных работ всё чаще в ход идут побочные продукты переработки древесины. Одним из наиболее распространённых стала ДВП.
Что это такое?
Расшифровка аббревиатуры ДВП — древесно-волокнистая плита. Это листовой стройматериал с демократичной стоимостью. Может иметь разные параметры плотности: бывает твёрдой, мягкой и полутвёрдой. Толщина в коридоре от 2 до 13 мм, у отдельных моделей — до 40 мм. Сырьём для производства ДВП становятся отходы деревообработки и лесораспила. Путём размола и пропаривания грубый материал перерабатывается до состояния волокон нужной структуры. В качестве основных связующих компонентов к ним добавляют полимерные смолы. Для увеличения параметров влагоустойчивости в древесно-волокнистую субстанцию вводят специальные добавки.
Выпуск ДВП считается одним из наиболее экономически выгодных методов использования отходов деревообработки.
Этот материал получил широкое распространение — его активно применяют в строительстве и облицовке внутренних помещений, обустройстве тепло- и шумоизоляции стен, создании мебели.
- высокая теплоизоляция;
- хорошее звукопоглощение;
- простота обработки;
- длительный эксплуатационный период;
- малые параметры веса и толщины при высоком уровне жёсткости;
- доступная цена;
- широкий размерный диапазон плит.
ДВП имеет износостойкое покрытие. Оно легко поддаётся уходу, его можно очищать любыми моющими средствами, в том числе агрессивными. Несмотря на внушительный перечень преимуществ будет неверным сказать, что ДВП – универсальный материал, у него имеются и свои минусы:
- низкая стойкость к поперечной нагрузке на изгибе;
- при покупке несертифицированного товара велик риск присутствия токсичных соединений в клеевой составляющей.
Особенности изготовления плит не позволяют выполнить их с одинаковой стойкостью на изгиб в разных направлениях. При поперечном сгибе не исключён излом плиты. Поэтому при изготовлении сложных конструкций, где необходимо выгибать радиус, действовать следует с большой аккуратностью. При обшивке вертикальных поверхностей с ДВП, материал надо прижимать к основанию максимально плотно, исключая образование зазоров — присутствие воздушных подушек часто приводит к заломам. Также следует иметь в виду, что древесно-волокнистые листы довольно тонкие, поэтому при сильном механическом воздействии могут разрушаться.
Производство
Сырьём для производства ДВП становятся любые отходы деревообработки:
- опилки;
- щепа;
- задревесневшие фрагменты стеблей прядильных культур.
Сырьё тщательно моется и очищается от любых посторонних примесей, потом подсушивается и поступает в дефибраторы и рафинаторы, где происходит его дробление. Величина помола бывает самой разной. Дальше материал прессуется, обычно используется мокрая либо сухая технология. Мокрый метод считается экологичным, поскольку расходуется меньше связующих компонентов. Иногда производство обходится вовсе без введения полимерных добавок. Однако, это трудоёмкий и энергоемкий процесс, поэтому на выходе материал получается более дорогим. На просушивание одного листа уходит порядка 15-20 минут – это существенно ограничивает производительность оборудования, соответственно, также влияет на себестоимость материала.
При мокрой прессовке в измельчённый древесно-волокнистый материал вводятся все основные добавки, а также вода.
Сырьё перемещают в дозатор, а оттуда ровным слоем выкладывает состав на сетчатую ленту.
Отдельные сорта ДВП во влажном прессовании изготавливаются без композитных добавок.
Для обеспечения максимального сцепления древесных волокон между собой сформированные плиты перемещаются в специальную камеру, где под воздействием повышенной температуры идёт дозревание материала. В ней листы лежат несколько часов до тех пор, пока волокнистый материал не станет крепким, прочным и однородным. Из камеры плиты выходят с минимальной влажностью и тут же принимаются интенсивно впитывать воду из воздуха — как следствие, края листов начинают загибаться. Чтобы не допустить деформации, материал тут же перемещают в другую установку, где его медленно доводят до оптимальной влажности. Лишь после этого материал поступает на установки для прокрашивания либо отправляется на полки магазинов.
Впервые техника создания ДВП была разработана ещё 200 лет назад. Изначально плиты получали без использования связующих компонентов. В 30-х гг. прошлого века была разработана мокрая техника, она позволила многократно повысить устойчивость и прочность готового материала.
Современная технология производства листов остаётся неизменной уже в течение полувека.
Сравнение с МДФ
За долгую историю выпуска ДВП производство было поставлено на поток, технология постоянно совершенствовалась. В отдельную линию было выделено изготовление МДФ. Невзирая на то, что и ДСП, и МДФ изготавливаются из отходов лесопереработки, тем не менее эти два материала отличаются. Разница, в первую очередь, касается исходного сырья. Так, для создания ДВП в ход идут отходы деревообработки; для изготовления МДФ используются целые деревья, предназначенные на вырубку, либо цельные куски древесины. ДВП изготавливают горячим прессованием стружек и опилок. В производстве МДФ прессуется измельчённая дисперсионная стружка.
На выходе МДФ получается влагостойким, такие материалы можно использовать в помещениях с высоким уровнем влажности.
ДВП под действием влаги довольно быстро разрушается.
Вреден ли материал для здоровья?
Каждый человек при выполнении ремонта в своём доме и покупке мебели старается приобрести только самые экологически безопасные материалы, чтобы оградить себя и своих родных от опасных для здоровья воздействий. Качественная ДВП имеет высокий класс безопасности. В качестве сырья используются только натуральные материалы — щепа или целлюлозные отходы. И те и другие являются абсолютно безвредными. В качестве связующих компонентов в древесно-волокнистую массу вводят:
- парафин;
- эмульсии синтетических смол;
- канифоль;
- битум;
- глинозём;
- пектол;
- гипс.
Все эти добавки не выделяют абсолютно никаких токсичных испарений.
Формальдегиды, которых так боятся потребители, уже давно запрещены для применения, и этот запрет подтверждён в соответствующем нормативном акте ГОСТ 4598-86. Вредные для жизни и здоровья вещества могут присутствовать только в «левой» продукции, выполненной с нарушением установленных нормативов.
А вот при горении отдельных компонентов могут выделяться нежелательные для человеческого организма компоненты и причинять вред здоровью. Так, если вы будете утилизировать ДВП через сжигание, то это может закончиться отравлением. Таким образом, древесно-волокнистая плита абсолютно безопасна, но лишь в том случае, если вы выбрали товар добросовестного производителя и правильно его эксплуатировали.
Обзор видов
По назначению выделяют древесно-волокнистые плиты общей и специализированной группы. Последние обладают особыми параметрами, их можно разбить на три категории:
- влагостойкие — в данном случае при изготовлении рабочей смеси в неё вводятся компоненты, повышающие стойкость к воде;
- трудносгораемые — изготавливаются с добавлением антипиренов, которые многократно уменьшают горючесть древесных плит;
- отделочные — такие ДВП задекорированы, обычно это окрашивание или оклеивание полимерной плёнкой с имитацией натурального материала (камня, кирпича либо древесины).
По характеристикам плотности выделяют следующие разновидности.
- ДВП мягкая — плиты с малой прочностью, сниженной теплопроводностью и повышенными параметрами плотности.
Толщина этих плит колеблется в коридоре 8-25 мм, параметр плотности — 150-350 кг/м3. Эти плиты не используют как базовый стройматериал, чаще они идут в ход для создания шумоизоляции основных стен, полов, а также потолков. Можно сказать, что это некий аналог ГКЛ, но более пластичный и простой в монтаже. Да и стоит такая установка намного дешевле, нежели ГКЛ аналогичных габаритов. Мягкие плиты можно уложить как подстилку под ламинат либо линолеум. При создании мягких плит полимерные связующие компоненты не применяют, соответственно, материал на 100% экологичен — именно поэтому его нередко покупают для облицовки комнат людей с аллергическими болезнями и детских помещений.
- ДВП полутвёрдая — в сравнении с мягкими листами, данная разновидность ДВП имеет чуть более высокие характеристики плотности и прочности, они соответствуют 450-750 кг/м3, при этом толщина листа колеблется в границах 6-13 мм. Эта разновидность ДВП нашла повсеместное распространение при создании задних стенок мебельных модулей, выдвижных полок шкафов и рабочих столов.
- ДВП твёрдая — уровень твёрдости таких ДВП варьируется в границах от 800 до 900 кг/м3. Толщина соответствует 2,5-6 мм. Такие плиты востребованы при выпуске мебельных конструкций.
- ДВП сверхтвёрдая — подобные листы характеризуются высочайшими параметрами плотности, она составляет примерно 950 кг/мз. Это высококачественный материал, простой в обработке и лёгкий в установке. Подобная прочность достигается за счёт введения в сырьевую массу пектола. Сверхтвёрдые ДВП нашли своё распространение при монтаже арок и межкомнатных перегородок. Кроме того, они актуальны при создании напольных покрытий. Ещё одна характеристика подобных плит — высокая электроизоляция позволяет использовать их для оборудования щитков и электропанелей.
Очень часто поверхность твёрдых древесно-волокнистых плит облагораживают меламиновыми или синтетическими плёнками, они имеют глянцевую либо матовую структуру или имитируют природные материалы. Декоративные ДВП характеризуются повышенной стойкостью к истиранию и действию влаги. За счёт уникальной технологии производства они имеют эстетичный вид. В ходе производства применяется техника многослойного нанесения покрытия на наружную поверхность. Плита сначала проходит предварительную обработку, потом на её верхний слой накладывается грунтовка, а после создаётся рисунок.
По оформлению выделяют множество других типов ДВП: кашированная, шпонированная, декорированная и шлифованная. Он может быть белой или цветной. Многие изделия имитируют текстуру натуральной древесины венге, камня либо кирпича. Декор может быть одно- и двухсторонним.
Размеры и вес
В зависимости от функционального предназначения предлагается несколько типов ДВП.
- Плиточный — как правило, имеет компактные габариты. Его продают в форме квадратов от 30х30 до 100х100 см. На торцах предусмотрен механизм шип-паз, это существенно упрощает монтаж плит.
- ДВП под вагонку — такие модификации повторяют габариты классической вагонки, имеют механизм шип-паз на торцах. Эти плиты характеризуются быстрым монтажом, устойчивостью к короблению и выглядят намного лучше, нежели пластиковая вагонка.
- Листовой — продаётся в стандартных типоразмерах. Его формат в точности соответствует характеристикам ГКЛ, ДВП и МДФ.
О размерах листовой ДВП можно говорить исключительно в связи с типовыми плитами и листами. В соответствии со стандартами толщина плиты может варьироваться от 2 до 40 мм. Все остальные параметры определяются следующим образом:
- ширина —1220 мм, 1700 мм;
- высота — 2140 мм, 2440 мм, 2745 мм.
Большинство фирм также выпускает неформатные листы. В ходе формования их подрезают, порой в функционировании оборудования происходят сбои и приходится обрезать края меньше или больше, чем обычно. Из-за этого листы могут получиться более короткими, хотя по качеству они практически ничем не отличаются. А вот цена на них намного ниже. Поэтому если типовой размер вам не принципиален — лучше отдать предпочтение «дефектным».
Популярные производители
В последние годы появилось много кустарных производств, на которых древесно-волокнистые плиты изготавливают без надлежащего контроля за качеством готовой продукции. Современный рынок переполнен панелями, которые могут содержать опасные для здоровья компоненты. Чтобы избежать неприятных последствий, отдавать предпочтение лучше всего известным маркам, зарекомендовавшим себя на рынке в качестве производителей продукции высочайшего качества.
- ЗАО «Изоплит» — уже почти пять десятилетий занимается выпуском листов ДВП.
- Княжпогостский завод — один из крупнейших изготовителей в России.
- ЛПК «Полеко» — производит экологичные ДВП на лигнине.
Продукция комбината отвечает самым жёстким требованиям западноевропейских стандартов, поэтому она продаётся не только в нашей стране, но и за рубежом.
- SteelBoard — ассортимент состоит из плит с уникальным параметром водопоглощения и разбухания.
Сферы использования
Стены
При планировании ремонтно-отделочных работ на любых вертикальных поверхностях обычно используют ламинированные ДВП. Они отличаются эстетичным дизайном, лёгкостью обслуживания, а также удобством обработки. Преимущества такого типа отделки очевидны:
- не нужно никакой дополнительной подготовки поверхностей, поскольку монтаж панелей выполняется на каркас из деревянного бруска либо металлопрофиля;
- для облицовки не нужен специальный инструмент или особые навыки работы;
- ДВП-панели для крепления на стенах обычно имеют механизм шип-паз, это существенно облегчает их состыковку;
- стеновые ДВП в готовом виде могут иметь имитацию древесины либо принт, при этом не требуют никаких дополнительных работ по облицовке.
Для обшивки вертикальных поверхностей можно использовать любую древесно-волокнистую панель с гладким покрытием. В таком случае на неё можно нанести любой другой облицовочный материал, включая обои. Кстати, несмотря на то, что поклейка обоев на ДВП — процесс весьма трудоёмкий и занимает немало времени, демонтаж устаревших покрытий не составляет никаких трудностей, и в этом несомненные достоинства материала перед гипсокартоном.
Из облагороженных ДВП часто делают фартук на кухне.
Пол
Это самый перегруженный элемент комнаты, поэтому использование любых листовых композитов нужно продумывать с учётом интенсивности эксплуатации покрытия. Чаще всего ДВП применяют при фиксации на уже существующее покрытие из досок, на лаги ДВП укладывают реже. В первом случае ДВП выполняют задачу выравнивания поверхности. Во втором выравнивание достигается за счёт лаг, но нагрузки на такую поверхность должны быть минимальными. Чаще всего древесно-волокнистые плиты применяются как подкладка под линолеум или другие напольные покрытия.
Потолок
Для облицовки потолочной поверхности можно использовать ламинированную плиту в чистом виде или под отделку. Во втором случае можно выполнить черновую отделку мягкой плитой – это многократно увеличивает шумопоглощение и теплоизоляцию. Кроме того, мягкая ДВП хорошо пропускает воздух. Древесно-волокнистые плиты для отделки потолочных поверхностей имеют свои преимущества:
- простота монтажа;
- экологичность;
- паропроницаемость.
Такие панели отличаются влагостойкостью, однако прямое попадание на них воды не рекомендовано.
В быту
Древесно-волокнистые плиты широко востребованы не только в строительстве, но также и в изготовлении мебели, монтаже дверей и всевозможных перегородок. Это прочный, но при этом лёгкий материал с большой площадью поверхности листа. ДВП часто покупают для изготовления ульев для пчёл. В таком случае деревянный каркас обшивают плитами ДВП, а промежутки заполняют любым утеплителем. Такие ульи существенно выигрывают у стандартных пчелиных домиков своей дешевизной — это особенно актуально в условиях большой пасеки.
Ещё одна сфера использования ДВП — изготовление мебели. Чаще всего материал идёт на заднюю стенку ящиков корпусных модулей. Словом, сфера использования обширная. Недостаток у плит только один — в условиях повышенной влажности без специальных гидрофобных добавок этот материал начинает деформироваться и разбухать, идёт волнами и при высыхании остаётся деформированным. Поэтому в неотапливаемых или сырых помещениях использование такой мебели не рекомендовано. Хотя некоторые марки с высокой влагостойкостью используют для обшивки балконов и уличных дверей.
Правила работы с плитами
Во время работы с ДВП возникает несколько вопросов — чем резать плиты, как их прикрепить и каким инструментом обрабатывать. К примеру, мало кто знает, как склеить плиты ДВП между собой — эпоксидный клей и жидкие гвозди зачастую не могут справиться с подобной задачей. В данном случае на помощь придут специальные составы для склейки ДВП или ПВА. Резать ДВП в бытовых условиях можно ножовкой по металлу или обычным монтажным ножом. Обращаем внимание на то, что лезвие обязательно должно быть как можно более острым. Распил выполняют аккуратными движениями – в противном случае велик риск срыва лезвия и получения травмы.
Особого рассмотрения заслуживает вопрос об облицовке поверхности древесно-волокнистых плит. Здесь возможны два варианта — покраска в разные цвета и поклейка обоев. ДВП плохо принимает влагу, другими словами, к поверхности древесно-волокнистых плит плохо прилипает краска. По этой причине перед окрашиванием плиту обязательно нужно грунтовать. Если вы планируете оклеить ДВП обоями, то сначала нужно промазать поверхность плиты краской, поскольку обойный клей может вызвать коробление, а уже на окрашенные поверхности клеить обои. Таким образом, можно использовать любые варианты отделки, но важно правильно подготовить поверхность панелей.
При эксплуатации изделий из древесно-волокнистой плиты на них могут появиться вмятины и царапины. Их заделывают просто: нужно только зашпаклевать повреждённую поверхность, а затем покрасить.
О том, чем правильно крепить ДВП, смотрите в следующем видео.
youtube.com/embed/hCZOzDCJ9DM?modestbranding=1&iv_load_policy=3&rel=0″/>
чем обработать плиты от влаги? Выбираем водостойкие ДВП-листы для пола
Дерево – это отличный надежный экологичный строительный и отделочный материал. Однако конечная продукция из него дорогая, к тому же в процессе ее изготовления образуется довольно высокий процент отходов. Сегодня существует широкий ассортимент современных материалов, выполненных из отходов деревообрабатывающей промышленности. Рассмотрим подробнее, что такое влагостойкая ДВП и чем пропитывают плиты для защиты от воды.
Особенности и сферы применения
Для изготовления материала используются древесные волокна. Ковер из них подвергают горячему прессованию или сушке, применяются связующие клейкие вещества и специальные добавки. Древесноволокнистая плита (ДВП) может иметь различные характеристики и области применения, которые зависят от добавок, способа изготовления, оформления поверхностей. Влагостойкая ДВП производится с добавлением канифоли и парафина.
ДВП находит широкое применение, так как обладает следующими положительными характеристиками:
- не подвергается деформациям, устойчиво держит размеры, что обеспечивает длительные сроки эксплуатации;
- имеет достаточную жесткость при небольшом весе и толщине листа, выдерживает несильные механические воздействия;
- хорошие свойства тепло- и звукоизоляции;
- материал легко поддается раскрою и обработке, прост для монтажа;
- умеренная стоимость делает его доступным для людей с не самым высоким уровнем доходов;
- при обшивке стен и потолков тонкий материал дает возможность экономить полезное пространство, а также сделать поверхности ровными, не применяя гипсокартон; кроме того, на плитах хорошо держится краска и декоративная штукатурка, прочая отделка;
- есть выбор плит по размерам;
- износоустойчивая поверхность, легко поддающаяся уходу, не боится воздействия бытовых химических веществ;
- независимо от вида обработки и марки изделия любая плита выдержит кратковременное воздействие влаги.
Идеальных вещей не существует, у ДВП также обнаруживаются недостатки, а именно:
- плиты не выдерживают поперечную нагрузку при изгибах;
- дешевые материалы изготавливаются с применением веществ, которые в дальнейшем при эксплуатации ДВП будут выделяться в окружающую среду и могут оказаться токсичными; использование такого продукта возможно только в хорошо вентилируемых помещениях.
Материал часто применяют при отделке как жилых и служебных, так и нежилых подсобных помещений. Разные виды плит можно укладывать на пол, стены, потолок. А также без ДВП не обходится производство мебели. Из него часто изготавливают задние стенки и перегородки шкафов, полки, выдвижные ящики для тумб и письменных столов.
Чем обрабатываются?
ДВП общего назначения характеризуется низкой влагостойкостью. При постоянном контакте с жидкостью она набухает, что ведет к ее разрушению. Чтобы плита могла нести нагрузку при условии повышенной влажности, производители вводят в ее состав специальные вещества. Кроме того, обработать от воздействия влаги можно и готовое изделие. На производствах чаще всего применяют ламинацию. На лист наклеивается специальная пленка, высокая температура и давление создают условия для полимеризации.
Ламинация не только обеспечивает защиту от влаги, но и от ультрафиолетовых лучей, высокой температуры.
Пропитать ДВП для влагостойкости можно и своими руками в домашних условиях. Строительные магазины предлагают специальные средства в большом ассортименте. Защитная пропитка также противостоит развитию плесени. Один из самых простых и доступных способов защитить материал от воздействия влаги – покрыть его краской на основе акрила. Краска послужит и для улучшения внешнего вида изделия. Разогретый парафин также может быть использован для обработки поверхности.
Водостойкая ДВП часто применяется для укладки на полу в помещениях, где бывает повышенная влажность, например, на кухне. А также такие изделия подойдут для облицовки стен в ванной. Ламинированные покрытия выпускаются в разных цветовых решениях, могут имитировать плитку, камень, кирпич. Это дает возможность оформить помещение в любом стиле.
Как выбрать?
При выборе ДВП нужно обратить внимание на следующие нюансы:
- прежде всего, нужно учесть, где вы собираетесь использовать материал; для применения в жилых помещениях понадобится продукт, не содержащий формальдегида, об этом будет свидетельствовать сертификат качества, наличие которого у продавца обязательно;
- далее нужно определиться с видом материала – для сырых помещений подойдет влагостойкая ДВП;
- в зависимости от цели использования (покрытие на пол, стенка в шкафчике) выбирайте плиты достаточной толщины и размера;
- не будет лишним проверить качество товара: должны отсутствовать пузыри, вздутия, масляные и парафиновые пятна, прочие повреждения;
- не стоит покупать товар, если на нем нет этикетки с необходимой информацией.
В следующем видео вы можете посмотреть рецепт универсальной влагоотталкивающей пропитки.
0773-2308-MTDC: ДВП и фанера
0773-2308-MTDC: ДВП и фанераМарт 2007 г. | 7300 | 0773-2308-MTDC |
Рича Уилсон, историк межгорной архитектуры
Кэтлин Снодграсс, руководитель проекта
Это
технический совет — второй из серии об инновационных строительных материалах, разработанных
в первой половине 20 века и обычно входили в состав Лесных
Служебные здания. Эта серия поможет вам идентифицировать материалы, описывая
их история, производство и физические характеристики. Эта серия также
решает распространенные проблемы и предоставляет рекомендации по техническому обслуживанию, ремонту и
замена.
Рисунок 1—Лакированная фанера покрывает
стены
и потолок лазарета Рабидо
, построенного в 1935 году.
Как указано в технической подсказке, здание начала 20-го века
Материалы: Введение (/t-d/pubs/htmlpubs/htm06732314/ Имя пользователя:
t-d Пароль: t-d), Лесная служба всегда поощряла использование
продукции на своих объектах.Уже в 1933 году приемлемые стены и потолок
продукты включали древесноволокнистые плиты (иногда называемые жесткими плитами, строительные
доска или стеновая плита) и фанера. Улучшение вашингтонского офиса
Справочник (1937 г.) и Принципы архитектурного
Планирование административных улучшений лесной службы (1938 г.) отмечено
что некоторые древесноволокнистые плиты были приемлемы для использования в качестве изоляции и для внутренней отделки помещений. стены и потолки. К ним относятся Masonite, Nu-Wood, Du-X и Fir-tex. К
поддержки цели Лесной службы по использованию древесины, предпочтение отдавалось древесноволокнистым плитам.
отделочный материал, хотя они также считались подходящими в качестве планки или основания
для гипсовой отделки.
Хотя первый американский патент на ДВП был выпущенный в 1858 году, ДВП не получил широкого распространения до тех пор, пока 1910-е годы. Во время Второй мировой войны производство увеличилось, потому что ДВП можно было легко и быстро установить во временном военные структуры. Производство древесноволокнистых плит также выросло вместе с спрос на жилье после войны, особенно в качестве внутренняя отделка. Некоторые древесноволокнистые материалы были изготовлены для наружного применения, но они часто работали плохо.
Фанера, еще один продукт на основе древесины, завоевала популярность благодаря технологическим
достижений во время Первой и Второй мировых войн.Его можно использовать для интерьера или экстерьера
применения в зависимости от типа клея, используемого в фанере. Посредством
В 1950-х и 1960-х годах предпочтение отдавалось фанере и ее двоюродному брату ДСП.
ДВП для многих применений.
ДВП
ДВП — это общее название строительных панелей из дерева или овощей. волокна. Некоторые из них представляют собой однородные материалы, а другие представляют собой ламинированные листы с сердцевины волокон и поверхности из измельченной древесины. Первые панели из ДВП были изготовлен из волокон из множества материалов, включая джут, солому, сахарный тростник стебли, лен, конопля, трава, газеты и скорлупа арахиса.Они были изготовлены под такими названиями, как Fir-tex, Homasote, Masonite, Beaver Board, Feltex, Nu-Wood, и Апсон Борд.
Древесина всегда была наиболее распространенным волокном, используемым в древесноволокнистых плитах. Историческое производство
процессы были разнообразными, но для большинства из них требовался процесс варки или измельчения
древесина, чтобы разделить ее волокна. Пульпу смешивали со связующими веществами, такими как клей,
асфальта или смол и перемещали на экраны, где сильное давление и высокая температура сжимали
из воды и сжал волокна. Этот процесс связывал древесные волокна с
между собой и переплетами, в результате чего одна сторона была гладкой, а другая — гладкой.
текстурированный, потому что он был прижат к экрану. Сформированные листы
были высушены, отделаны, а в некоторых случаях отделаны краской, эмалью, бумагой,
ткань или глазурь. В конце концов, были разработаны процессы для покрытия панелей
с деревянным шпоном или пластиковым ламинатом.
Поскольку влага была их главным врагом, древесноволокнистые плиты часто обрабатывали гидроизоляционные материалы для замедления гниения и набухания.Асбест, гипс, в некоторые смеси добавляли глину, скипидар, парафин или другие материалы. для улучшения огнестойкости и получения других желательных качеств, таких как жесткость, твердость, гладкие поверхности, повышенная прочность или долговечность.
Изделия из ДВП ценились за простоту использования, особенно неквалифицированными специалистами.
рабочие. Для Лесной службы это было особенно важно в молодости,
необученные люди из Гражданского корпуса охраны природы строили объекты. В отличие от оштукатуренных стен и потолков, ДВП можно было наносить быстро и
не требует времени на высыхание. В «Справочнике по совершенствованию» (1937 г.) указывалось, что для
из соображений экономии ДВП рекомендовалось для отделки чердаков, подвалов,
и шкафы, даже когда другие помещения были оштукатурены.
Стыки между панелями из ДВП можно обрабатывать несколькими способами. Принципы
Архитектурного планирования для административных улучшений лесной службы (1938 г.) продвигал соединение с V-образной канавкой (рис.
2), а не более распространенная практика
покрытия стыков рейками.Строительство Северного региона
и Руководство по техническому обслуживанию (1935 г.) рекомендовали устанавливать Masonite или фанеру горизонтально.
на стенах с накладкой рейки кресла по горизонтальному шву между листами.
Если эти стеновые панели были установлены в жилых помещениях, в справочнике рекомендовалось покрывать их лаком.
их. В других зданиях мазонитовые панели должны были быть отделаны светлыми тонами. кальцимин. Кальцимин — недорогая краска на водной основе (иногда называемая темперой).
содержащие клей и краситель.
ДВП различают по плотности.Большинство исторических древесноволокнистых плит можно разделить на категории как плита низкой плотности (изоляционная), плита средней плотности или ДВП.
Рис. 2. Этот раздел на стр. 24
«Принципы архитектурного планирования
лесной службы для административных улучшений лесной службы» (1938 г.) объясняют
допустимое использование фанеры, мазонита, ну-дерева и подобных материалов.
Древесноволокнистая плита низкой плотности
Древесноволокнистая плита низкой плотности была известна как изоляционная плита из-за ее звукопоглощающих свойств. и термические качества.Это легкий, жесткий продукт из волокнистой целлюлозы. был доступен в листах, досках и плитках. Лучше всего подошла теплоизоляционная плита. для внутреннего применения из-за его восприимчивости к повреждению водой.
Изоляционная плита может быть установлена на внутренних стенах и потолках и окрашена
или кальцинированные. Оставленный незавершенным, его коричневое лицо можно было легко поцарапать или разрезать.
для создания интересных узоров (рис. 3), а затем окрашены, чтобы обеспечить легкость
очищенная поверхность (рис. 4). Листы со скошенными краями были в наличии и предлагались
дополнительные декоративные свойства.Иногда теплоизоляционная плита, а не традиционная
деревянная рейка, использовалась для поддержки штукатурки.
Рисунок 3—Этот потолок из фибрового картона на станции рейнджеров Бьютт-Фолс
(Rogue
Национальный лес Ривер-Сискию,
Тихоокеанский Северо-Западный регион) был вырезан в
декоративный узор
. Потолок — натуральный коричневый
цвет древесной массы.
из которого он был изготовлен.
Рисунок 4—Потолок из ДВП в офисе Fenn Ranger
Station (Moose
Creek Ranger District, Национальный лес Нез-Персе
, Северный регион)
вырезаны и раскрашены.
В то время как толщина изоляционной плиты варьировалась от 3⁄8 до 1 дюйма, Forest
В руководствах по обслуживанию часто рекомендуются ½-дюймовые изоляционные плиты для помещений. Листы были от 4 до 8 футов в ширину и могли быть до 16 футов в длину. Панели, используемые в качестве
изоляционная планка под штукатуркой обычно имеет ширину от 18 до 24 дюймов и 48
дюймов в длину. Теплоизоляционная плита была прикреплена к каркасу здания с помощью клея,
гвозди, шурупы или запатентованные методы, такие как металлические решетки для потолка,
предшественник подвесных потолков, которые сегодня можно найти во многих офисах.
Ранние торговые названия изоляционных плит включали Insulate, Fir-tex и Nu-Wood — все из которых изготовлены из древесной массы. В 1921 году древесноволокнистая плита была произведена с использованием багасса, побочный продукт сухой мякоти сахарного тростника после извлечения сока. Эта древесноволокнистая плита была первой из многих продуктов, разработанных компанией Celotex Co., которая позже произведены акустические материалы, такие как перфорированный Acousti-Celotex Cane. Кафельная плитка.
Первым продуктом Masonite, изготовленным в 1927 году, была изоляция толщиной 7/16 дюймов. плита, которая может быть использована в качестве структурной обшивки, звукоизоляции и
поверхность внутренней стены.Гипс, содержащий не более 10 процентов извести, может
быть нанесены непосредственно на плату. Другие ранние изделия Masonite включали скошенные
плитка, доски и плита Litecol, почти белая.
Masonite Corp. использовала уникальный процесс производства целлюлозы. Вместо варки или измельчения щепы, машина взорвала их с такой силой, что древесные волокна разделены. Позже Masonite Corp. сосредоточилась на производстве своего популярного оргалита. (см. раздел ДВП).
Древесноволокнистая плита средней плотности
Homasote, Beaver Board и Upson Board были средней плотности.
древесноволокнистые плиты, предназначенные для использования в различных областях.Хомасоте, представлен
в 1916 году представлял собой однородный материал из переработанных газет (источник
серого цвета) и нефтяной воск. Рекламируется как изоляционный и конструкционный
плита для внутренних и наружных работ, она была доступна как гладкая, рифленая,
или панели с текстурой дерева и как скошенный сайдинг. Панели размером от 8 на 14 футов
устранена необходимость в рейках или швах в большинстве комнат. Homasote все еще производится
сегодня.
Beaver Board был ламинированным листовым продуктом, изобретенным в 1903 году и усовершенствованным.
с несколькими патентами в 1910-х годах.В патенте 1914 г. описывалась пластина толщиной 3⁄16 дюйма.
доска с внутренним слоем измельченной древесины, покрытой тонкими слоями вареной
дерево с каждой стороны для обеспечения влагостойкости и прочности. Одна сторона была
отделка тонким слоем текстурированной шлифованной древесины в декоративных целях.
Эта версия Beaver Board, использовавшаяся в 1920-х годах, выпускалась с диагональю 32 и 48 дюймов.
ширины. На обороте был штамп с логотипом компании и инструкциями,
в то время как передняя часть имела галечную отделку, которую можно было красить, морить или оставлять
естественный.Чтобы обеспечить расширение, панели должны были быть установлены на 1/8 дюйма.
отдельно. Декоративные рейки обычно закрывали щель.
Upson Board была еще одной ламинированной древесноволокнистой плитой с одной текстурированной стороной, аналогичной по внешнему виду до Beaver Board. Основное отличие заключалось в том, что задняя часть На доске Upson Board не было штампа с названием торговой марки. Вместо этого его центральный слой был окрашен в синий цвет, что делало его легко узнаваемым. Три ширины (32, 48 и 64). дюймов) и семь длин были доступны. В 1920 году производитель запатентовал Upson Self-Clinching Fastener, стальная застежка с пятью зубцами.Это были были прибиты к шпилькам, а панели ДВП были прижаты к штырям, которые удерживал их на месте.
В течение нескольких десятилетий древесноволокнистые плиты средней плотности оставались популярными, несмотря на то, что их
изменились производственные процессы и ингредиенты. В 1928 году CertainTeed Corp.
купила Beaver Board Co. и продолжила производство Beaver Board в рамках этой торговли.
имени до начала 1940-х гг. Upson Co. ненадолго использовала это имя после покупки
Фабрика Beaver Board от CertainTeed в 1955 году. Они продолжали производить Upson.
картон, ДВП Beaver Universal и ДВП Beaver.Оригинальный Апсон
Компания закрыта в 1984 году.
ДВП
Самый исторический оргалит имел толщину от 1⁄8 до 5⁄16 дюймов, хотя два доски можно было склеить, чтобы сделать панель более жесткой. масонит Corp. представила свой первый оргалит в начале 1930-х годов. ДВП Presdwood, толщиной от 1⁄10 до 5⁄16 дюймов, использовался для внутренней отделки и как рейки поверх других продуктов Masonite. Панели могут быть прибиты гвоздями или склеены вертикально или горизонтально, затем окрашены или оклеены обоями.Известен более прочный продукт поскольку Tempered Presdwood был представлен в 1931 году. Часто его прикручивали к шпилькам. стыки покрыты декоративными планками. Temprtile, популярный выбор Для ванных комнат и кухонь использовалась водостойкая плита Masonite с тиснением. выглядеть как плитка размером 4 на 4 дюйма (рис. 5).
Рисунок 5—Temprtile, продукт из твердого картона с тиснением, напоминающим плитку
используется в качестве водостойкой обшивки
в ванной комнате повара в Fenn
Станция рейнджеров.
Masonite и другие древесноволокнистые плиты стали основным продуктом для производства сборных домов и украшали интерьеры более 150 000 хижин Quonset во время Второй мировой войны (рис. 6). К 1950-м годам сайдинг из ДВП был доступен в виде панелей, внахлест, гонт, и доски и дощатые стили. Дополнительные функции включали нанесенные на заводе грунтовки, вентилируемые монтажные планки и несколько текстур. Еще один продукт Masonite 1950-х годов. была серая внутренняя стеновая панель с текстурой под дерево, известная как Misty Walnut. масонитов Royalcote с его полированной и прочной отделкой из искусственного дерева также оказался популярным.
Рисунок 6 — Мазонит часто использовался для отделки интерьеров
Quonset
хижины, которые Лесная служба приобрела
у военных после Второй мировой войны.
Эта хижина Quonset под номером
теперь используется для хранения на административном объекте Duck Creek.
(район Джуно-Рейнджер, национальный лес Тонгасс, регион Аляска).
Идентификация панелей из ДВП
Древесноволокнистые плиты обычно можно определить по коричневому или серому цвету и однородности. внешний вид.Если ДВП окрашены, ищите такие признаки, как молдинги, скошенные стыки или задиры. Проверьте такие области, как подвальные лестницы и чердаки. там, где могут быть открыты неокрашенные поверхности. Вы можете увидеть поперечные сечения где древесноволокнистая плита была сломана или вырезана для электрических коробок, сантехники линии или механическое оборудование.
При постукивании изоляционная плита звучит несколько полой и мягче, чем гипс.
доска или штукатурка, хотя многочисленные слои краски могут минимизировать эту разницу.Если вы не можете определить, является ли поверхность ДВП, используя описанные методы
выше, выберите скрытую область (шкаф или под карнизом, например) и
просверлите небольшое отверстие, желательно ручной дрелью. Это поможет вам определить
толщину доски и обеспечит сверление стружки, которую можно исследовать
для цвета, текстуры и материала.
Техническое обслуживание и ремонт ДВП
Древесноволокнистые плиты имеют несколько общих проблем, но подвержены повреждению влагой. является наиболее распространенным.Теплоизоляционная плита более восприимчива к влаге. чем более плотный ДВП, хотя все изделия из ДВП могут коробиться или гнить в во влажных помещениях или при попадании в них воды. Держите ДВП сухими. Чистый протрите их влажной тканью и вытрите лишнюю влагу чистой тканью. Не используйте мыло или агрессивные моющие средства, если поверхность не покрыта краской или другим защитная отделка.
Поскольку изоляционные плиты относительно мягкие, на них можно помять или проколоть без труда. ДВП хрупкий.В любом случае незащищенные края и углы изделия из ДВП особенно уязвимы. Подумайте об установке пластика. угловые ограждения, дверные бамперы и другие защитные устройства. Расставить мебель и размещайте светильники таким образом, чтобы свести к минимуму контакт со стенами из ДВП.
Если ламинированные слои стеновой панели расходятся, их можно снова прикрепить
нанесение или инъекция пшеничной пасты, клея, обычно используемого при консервации
работать, потому что изменения могут быть отменены относительно легко. Вы можете сделать свой
паста собственного приготовления с пшеничным крахмалом из магазина натуральных продуктов (рецепт смотрите ниже),
хотя может быть проще купить пшеничную пасту из художественной или архивной продукции
поставщик. Если волокна стеновой панели расходятся:
- Жидкая пшеничная паста с водой.
- Используйте разбавленную пасту, чтобы пропитать область.
Этот подход подходит для небольших площадей. При значительных повреждениях может потребоваться замена стеновая панель.
Все древесноволокнистые плиты расширяются и сжимаются от влажности и должны быть установлены с зазорами между панелями.Слишком маленькие зазоры могут привести к тому, что плата деформация или отделка потерпеть неудачу. Если ДВП были установлены со слишком маленьким зазор, тщательно обрежьте древесноволокнистые плиты, чтобы оставить достаточно места для расширения.
Если деформировавшуюся панель ДВП можно снять без повреждений, слегка намочите ее,
приложите давление, чтобы сгладить его, и дайте ему высохнуть перед повторной установкой. Использовать
небольшие незаметные гвозди или шурупы при повторном креплении провисшей ДВП на
потолки.
Если древесноволокнистая плита слишком повреждена для ремонта, замените ее.ДВП по-прежнему сделал сегодня. Некоторые современные продукты соответствуют размерам и внешнему виду некоторых исторических продукты. Другой вариант — повторно использовать ДВП из менее заметного места (например, как чулан или чердак) или из построек, не имеющих исторического значения. Материалы-заменители, такие как гипсокартон, могут быть приемлемой заменой. для крашеных стеновых панелей. Обязательно проконсультируйтесь со своим персоналом по наследию и Управление по сохранению исторического наследия перед удалением или заменой каких-либо материалов.
Фанера
Большинство людей знакомы с фанерой, ламинированным изделием, состоящим из тонких
слои древесины, склеенные вместе с чередующейся перпендикулярной ориентацией волокон.Примерно до 1919 года фанера также была известна как чешуйчатая доска, клееная древесина и сборная древесина. древесина. Фанера легче и прочнее, чем массивная древесина, более гибкая и прочная.
имеет высокое значение сдвига.
В девятнадцатом веке фанеру делали из тонких полос распиленной древесины. и обычно использовался для изготовления мебели и дверных панелей. Фанерная промышленность начал процветать после изобретения вращающихся резаков в 1890-х годах. Эти машины разрезать большие тонкие листы дерева, вращая бревно против ножа.Это продвижение позволило разработать более крупные и прочные листы фанеры.
Несмотря на значительное внимание, производство фанеры в начало 1900-х годов. Это изменилось во время Первой мировой войны, когда продукт был улучшен. и использовался для постройки легких самолетов. Благодаря этим достижениям общественное мнение сдвинутый. Фанера, которая больше не рассматривалась как дешевый заменитель, стала цениться в разнообразие применения в строительстве.
Лаборатории лесных товаров Лесной службы приписывают значительные
вклад в технологию фанеры. Лаборатория приступила к испытаниям фанерной обшивки
в конце 1920-х годов и успешно построил экспериментальный фанерный завод с усиленной обшивкой.
дом в 1935 году. Два года спустя Лаборатория лесных товаров построила первый
сборный недорогой дом из фанеры.
Ряд других новинок появился в 1930-х годах для ламинированного листового материала. К ним относятся внедрение первой водостойкой фанеры для наружных работ. использование (1934 г.), первый коммерческий сборный дом с наружной фанерой. (1936 г.) и дизайн фанерного дома Dri-Bilt (1938 г.) с PlyScord. черновые полы и обшивка, потолки и стены PlyWall, встроенные панели PlyPanel и Фасад PlyShield используется в более чем миллионе недорогих домов.Фанера стала общепринятым строительный материал.
Первые стандартные листы фанеры были 3 на 6 футов, но к началу
1930-е годы стандартными были листы размером 4 на 8 футов. Обычно их было нечетное количество.
слоев, хотя фанера с четным числом слоев производилась с тех пор
Вторая Мировая Война. По мере совершенствования технологий изготовления фанеры производители
все чаще предлагается фанера с декоративным шпоном и отделкой. Некоторые были
выполнены с исчерченными в них бороздками или V-образными канавками.Другие были рельефными
или готовые в нескольких цветах.
Первоначально ограничивался дверными панелями, стенами и потолками (рис. 7), фанера в конечном итоге был принят в других приложениях, таких как обшивка и краснодеревщики. (рис. 8), так и наружные обработанные поверхности.
Рисунок 7—Интерьер лазарета в Рабидо
CCC лагерь
(недавно
обозначен как национальный
Историческая достопримечательность)
отделана лакированной фанерой,
включая изогнутые своды
в коридоре и некоторые
номера.Лагерь Рабидо является частью
Блэкдака
Рейнджер
Район (Национальный лес Чиппева, Восточный регион).
Рисунок 8—Эти фанерные шкафы, изготовленные CCC
на кухне
на станции Fenn Ranger, находятся на кухонной стороне
прилавка. В этой конструкции шкафы, видимые
только повару, выполнены из фанеры, а шкафы
видно из столовой
построены из массивного бруса.
Идентификация
Наиболее очевидные характеристики фанеры включают текстуру древесины, ламинирование слои и заглушки в форме футбольного мяча, используемые в качестве заплат при удалении дефектов из слоя.Часто эти заглушки видны даже после того, как фанера была окрашены.
Фанерабыла доступна с клеем для внутренних, наружных или морских целей. с конца 1930-х гг. Интерьерные клеи остаются самыми дешевыми, но морские клеи обеспечивают наибольшую устойчивость к расслаиванию (разделению слоев), если фанера промокает. Обычно на фанере клеймят ее прочность и эксплуатационные характеристики.
Техническое обслуживание и ремонт
Фанера так же долговечна, как массивная древесина, если выбран правильный тип и
он правильно поддерживается.За фанерой для интерьера можно ухаживать так же, как за ДВП. Регулярно вытирайте пыль или протирайте влажной тканью. Наружная фанера требует профилактики
техническое обслуживание для защиты от гниения, расслоения, деформации и атмосферных воздействий.
Свести к минимуму возможность повреждения, поддерживая в чистоте водосточные желоба и водосточные трубы,
убедитесь, что земля находится не менее чем на 8 дюймов ниже фанерного сайдинга, и удалите
соседний мусор и растительность, удерживающие влагу. Убедитесь, что внешняя отделка – будь то
это краска, морилка или другой материал – поддерживается в хорошем состоянии благодаря
регулярное техническое обслуживание и повторное применение.Выветрившуюся фанеру можно слегка отшлифовать
и запечатаны.
Большинство поломок материалов происходит из-за использования фанеры, изготовленной с использованием внутренних клеев.
во внешних приложениях. Клей выходит из строя, и слои расходятся. Если
слои начали расходиться, но панель в целом цела, слои
можно переклеить с помощью большого шприца (продается в ветеринарных магазинах)
между ними ввести клей для дерева. В качестве альтернативы можно использовать канцелярский нож.
используется, чтобы прорезать щель в верхнем слое и приподнять ее ровно настолько, чтобы нанести клей
между ним и следующим слоем.Либо зажать слои (если панель вертикальная)
или положите на поверхность мешок с песком или другой тяжелый предмет (если панель расположена горизонтально)
пока клей не высохнет. Если расслоение обширное, панели может потребоваться
заменить.
Фанера, установленная без зазора между соседними панелями, может деформироваться при он расширяется. Тонкие листы, которые погнулись, иногда можно выпрямить с помощью дисковой пилы аккуратно срежьте узкую полоску на стыке. Более возможно, потребуется добавить крепеж.Более толстые панели, вероятно, придется заменить.
Фанера, имеющая незначительные повреждения от ударов, обычно может быть отремонтирована с использованием дерева.
замазка. Обязательно используйте замазку, предназначенную для данного приложения. Наружная шпаклевка и
имеются шпаклевки под покраску. Некоторые шпаклевки оставляют пятна, но проверьте
замазку перед использованием, чтобы убедиться, что вылеченный и окрашенный участок будет соответствовать
окружающая поверхность. Если повреждение от удара обширное или если оно затрагивает
прочность панели, замена — лучший вариант.
Вы можете лечить гнилую фанеру, удаляя некачественные участки и заменяя их с соответствующей фанерой. Нанесите консервант для дерева, краску или другие защитные герметик по мере необходимости потом.
Фанера легкодоступна, поэтому замена панелей соответствующими материалами
может быть легко, если поверхность гладкая и покрыта краской. Это может быть больше
трудно подобрать специальные покрытия, такие как тиснение, бороздки и канавки.
Если фанера имеет прозрачную отделку, важно, чтобы порода, текстура,
и другие визуальные характеристики оригинальной фанеры.Это также важно
чтобы соответствовать типу прозрачной отделки, потому что разные отделки стареют по-разному.
Например, лак со временем желтеет, а полиуретан на водной основе остается. прозрачные, а масляные покрытия темнеют.
Сегодня фанерная обшивка вытесняется ориентированно-стружечными плитами (OSB), его более дешевый кузен, разработанный в конце 1970-х годов. ОСБ не годится заменить открытые фанерные поверхности в исторических зданиях, потому что это характерная фактура поверхности.
Дополнительная информация
Следующие ресурсы содержат подробную информацию о ДВП и фанере.
Книги и журналы
Бюллетень APT 28, № 2–3. 1997. Содержит три статьи по Homasote, Masonite, Beaver Board и Upson Board.
Байнум, Ричард Т. 2000. Справочник по изоляции. Нью-Йорк: McGraw-Hill Professional. Включает главы, посвященные изоляционным плитам и историческим продуктам, а также каталог товаров с производителями и описаниями.
Шут, Томас С., изд. 1995. Строительные материалы двадцатого века. Нью-Йорк: Макгроу-Хилл.Имеет отдельные главы по ДВП, фанере и акустическим материалам.
Селлерс, Терри-младший, 1985 г. Фанера и клеевые технологии. Нью-Йорк: Марсель
Dekker, Inc., посвящена истории, производству и применению фанеры.
Другие ресурсы
Американская ассоциация древесноволокнистых плит
853 North Quentin Rd. № 317 Палатин, Иллинойс
60067
Телефон: 847–934–8394
Электронная почта: [email protected]
Веб-сайт: http://www.fiberboard.org/
APA—The Engineered Wood Association
7011 South 19th Ave.
Tacoma, WA 98466
Телефон: 253–565–6600
Электронная почта: [email protected]
Веб-сайт: http://www.apawood.org/
Ассоциация композитных панелей
18922 Premiere Ct.
Gaithersburg, MD 20879–1574
Телефон: 301–670–0604
Электронная почта: [email protected]
Веб-сайт: www.pbmdf.com
Лаборатория лесных товаров
One Gifford Pinchot Dr.
Madison, WI 53726
Телефон: 608–231–9200
Веб-сайт: http://www.fpl.fs.fed.us/
Ассоциация фанеры и шпона твердых пород
1825 Michael Faraday Dr.
Reston, VA 20190
Телефон: 703–435–2900
Веб-сайт: http://www.hpva.org
Благодарности
Авторы ценят готовность Марка Эллиса, Rogue River-Siskiyou Национальный лес, Керри Роепке, Национальный лес Тонгасс и Билл Юрд, Чиппева National Forest, чтобы сделать фотографии, чтобы проиллюстрировать этот технический совет.
Большое спасибо д-ру Джеррольду Э. Винанди из Лаборатории лесных товаров за его обзор и полезные комментарии по содержанию этого технического совета.
Часть исторической информации в этом техническом совете была получена от Plywood Веб-сайт Ассоциации пионеров, http://www.apawood.org/plywoodpioneers/.
Об авторах
Рича Уилсон, межгорный региональный историк архитектуры и заместитель председателя.
из совета директоров некоммерческого Института традиционных строительных навыков.
Имеет степень бакалавра в области архитектуры и степень магистра
в исторической сохранности. Будучи волонтером Корпуса мира, Рича возглавляла
Секции строительной инспекции в Блантайре, Малави, и предоставил архитектурные
услуги Habitat for Humanity и Save the Children. Она работала в частном порядке
практиковаться в Вашингтоне, округ Колумбия, и Орегоне, прежде чем поступить в Лесную службу в
1998.
Кэтлин Снодграсс пришла в MTDC в качестве руководителя проекта в 2001 году. из Университета штата Вашингтон в 1974 году со степенью бакалавра наук. в архитектурных исследованиях, а затем провел около 10 лет в проектировании дорог и строительство с Отделом автомобильных дорог Айдахо. Она начала свою карьеру с Лесной службы в 1984 году. Кэти работала в сфере благоустройства, ландшафтной архитектуры, наземная линия и общее инженерное дело в Национальном лесу Нез-Персе на протяжении около 10 лет и около 7 лет был архитектором лесных объектов. до прихода в MTDC.
Можно заказать дополнительные отдельные копии этого документа.
от:
Лесная служба Министерства сельского хозяйства США
Центр технологий и разработок Миссулы
5785 Hwy. 10 West
Missoula, MT 59808–9361
Телефон: 406–329–3978
Факс: 406–329–3719
Электронная почта: wo_mtdc_pubs@fs. fed.us
Для получения дополнительной информации о ранних строительных материалах,
связаться с Ричей Уилсон по телефону:
Телефон: 801 –625–5704
Факс: 801–625–5229
Электронная почта: [email protected]
или
обращайтесь к Кэти Снодграсс в MTDC:
Телефон: 406-329-3922
Факс: 406-329-3719
Электронная почта: ksnodgrass@fs.федерал.нас
Электронные копии MTDC
документы доступны в Интернете по адресу:
/rus/t-d.php
Сотрудники Лесной службы и Бюро землеустройства
может искать более полную коллекцию MTDC
документы, видео и компакт-диски во внутренних компьютерных сетях по адресу:
http://fsweb.mtdc.wo.fs.fed.us/search/
Лесная служба Министерства сельского хозяйства США (USDA) разработала
эта информация для руководства ее сотрудников, ее подрядчиков и ее
сотрудничающими федеральными и государственными агентствами и не несет ответственности за интерпретацию
или использования этой информации кем-либо, кроме ее собственных сотрудников. Министерство сельского хозяйства США (USDA) запрещает дискриминацию во всех
свои программы и мероприятия на основе расы, цвета кожи, национального происхождения, возраста,
инвалидность и, где применимо, пол, семейное положение, семейное положение, наличие родителей
статус,
религия, сексуальная ориентация, генетическая информация, политические убеждения, репрессалии,
или потому, что весь или часть дохода физического лица получена от какого-либо государственного
программа помощи.(Не все запрещенные основания применимы ко всем программам.) Лица
с ограниченными возможностями, которым требуются альтернативные средства для передачи программы
информации (шрифт Брайля, крупный шрифт, аудиозапись и т. д.) следует обращаться в Министерство сельского хозяйства США.
|
Топ |
ДВП | Encyclopedia.com
Справочная информация
Композитные лесоматериалы или инженерная древесина относятся к материалам, изготовленным из дерева, которые склеены вместе. В Соединенных Штатах ежегодно производится около 21 миллиона тонн (21,3 миллиона метрических тонн) композитной древесины.К наиболее популярным композиционным материалам относятся фанера, столярные плиты, ДВП, ДСП и клееный брус. Большинство этих продуктов основано на том, что ранее было древесными отходами или малоиспользуемыми или некоммерческими породами. При производстве композитов теряется очень мало сырья.
Древесноволокнистая плита средней плотности (МДФ) — это общий термин для панели, состоящей в основном из лигноцеллюлозных волокон в сочетании с синтетической смолой или другой подходящей связующей системой и скрепленных вместе под воздействием тепла и давления.Панели сжимаются до плотности от 0,50 до 0,80 по удельному весу (31-50 фунтов/фут3). Во время производства могут быть введены добавки для улучшения определенных свойств. Поскольку древесноволокнистую плиту можно разрезать на самые разные размеры и формы, у нее множество применений, включая промышленную упаковку, дисплеи, экспонаты, игрушки и игры, мебель и шкафы, стеновые панели, молдинги и дверные детали.
Поверхность МДФ ровная, гладкая, однородная, плотная, без сучков и зернистости, что делает отделочные работы более простыми и однородными.Однородная кромка МДФ позволяет выполнять сложные и точные методы обработки и отделки. Отходы обрезков также значительно сокращаются при использовании МДФ по сравнению с другими подложками. Улучшенная стабильность и прочность являются важными преимуществами МДФ, при этом стабильность способствует соблюдению точных допусков в точно вырезанных деталях. Это отличная замена массивной древесине во многих интерьерах. Производители мебели также чеканят поверхность объемными рисунками, поскольку МДФ имеет такую ровную текстуру и стабильные свойства.
За последние 10 лет рынок МДФ в США быстро вырос. Отгрузки увеличились на 62%, а мощность завода выросла на 60%. Сегодня в Америке ежегодно потребляется более миллиарда квадратных футов (93 миллиона квадратных метров) МДФ. Мировые мощности MDF увеличились на 30% в 1996 году до более чем 12 миллиардов квадратных футов (1,1 миллиарда квадратных метров), и в настоящее время действует более 100 заводов.
История
МДФ был впервые разработан в Соединенных Штатах в 1960-х годах, производство началось в Депости, штат Нью-Йорк.Похожий продукт, оргалит (спрессованная древесноволокнистая плита), был случайно изобретен Уильямом Мейсоном в 1925 году, когда он пытался найти применение огромному количеству древесной щепы, выбрасываемой лесопильными заводами. Он пытался впрессовать древесное волокно в изоляционную плиту, но изготовил прочный тонкий лист, забыв выключить свое оборудование. Это оборудование состояло из паяльной лампы, печатного станка восемнадцатого века и старого автомобильного котла.
Сырье
Древесная щепа, стружка и опилки обычно составляют сырье для древесноволокнистых плит.Однако, поскольку вопросы вторичной переработки и защиты окружающей среды становятся нормой, также используются макулатура, кукурузные рыльца и даже багасса (волокна сахарного тростника). Другие материалы также перерабатываются в МДФ. Одна компания использует сухие отходы
в размере 100 000 тонн в год. Помимо древесных отходов, на этом предприятии используется картон, картонная тара из-под напитков, содержащая пластмассу и металл, телефонные справочники и старые газеты. Синтетические смолы используются для соединения волокон вместе, а другие добавки могут использоваться для улучшения определенных свойств.
Производство
Процесс
Передовые технологии и обработка улучшили качество древесноволокнистых плит. К ним относятся инновации в подготовке древесины, рецепты смол, технология прессования и методы шлифования панелей. Усовершенствованная технология прессования позволила сократить общие циклы прессования, а антистатическая технология также способствовала увеличению срока службы ленты в процессе шлифования.
Подготовка древесины
- 1 Производство качественных древесноволокнистых плит начинается с выбора и очистки сырья, большая часть которого перерабатывается из стружки и стружки, получаемых на лесопильных и фанерных заводах.Сырье сначала очищают от любых металлических примесей с помощью магнита.
Далее материал разделяется на крупные куски и мелкие хлопья. Хлопья разделяются на штабеля опилок и щепы.
- 2 Материал снова проходит через магнитный детектор, при этом отбракованный материал отделяется для повторного использования в качестве топлива. Хороший материал собирается и отправляется в бункер для предварительного пропаривания. В бункер впрыскивается пар для нагрева и смягчения материала. Волокна подаются сначала в боковой шнековый питатель, а затем в поршневой шнековый питатель, который сжимает волокна и удаляет воду.Затем сжатый материал подается в рафинер, который разрывает материал на пригодные для использования волокна. Иногда волокно может пройти вторую стадию очистки, чтобы улучшить чистоту волокна. Моторы большего размера на рафинерах иногда используются для отсеивания посторонних предметов из процесса.
Отверждение и прессование
3 Смола добавляется перед стадией рафинирования, чтобы контролировать устойчивость смеси к формальдегиду, а после рафинирования добавляется катализатор.
Затем волокна выдуваются в сушилку с испарительной трубкой, которая нагревается либо маслом, либо газом.Соотношение твердой смолы и волокна тщательно контролируется путем взвешивания каждого ингредиента. Затем волокно проталкивают через скальпирующие валки для получения мата одинаковой толщины. Этот мат проходит несколько этапов прессования, чтобы получить более удобный размер, а затем обрезается до желаемой ширины перед окончательным этапом прессования. Пресс непрерывного действия, оснащенный большим барабаном, равномерно сжимает мат, контролируя его высоту. Прессы оснащены электронным управлением для обеспечения точной плотности и прочности.Полученная плита перед охлаждением разрезается на соответствующую длину с помощью пил.
Прессы имеют уравновешенные системы одновременного закрывания, в которых используются гидравлические цилиндры для выравнивания плиты, что при работе в сочетании с четырехточечным управлением положением обеспечивает больший контроль толщины отдельных панелей.
Гидравлическая система может закрывать пресс на таких скоростях и давлениях, которые уменьшают проблемы с предварительным затвердеванием плит и сокращают общие циклы прессования.
Шлифование панелей
- 4 Для получения гладкой поверхности панели шлифуются с помощью лент с абразивным покрытием.Обычно используется карбид кремния, но с учетом требований к более тонкой поверхности используются другие керамические абразивы, в том числе оксид циркония и оксид алюминия. Восьмиголовочное шлифовальное оборудование и двусторонняя планировка улучшают постоянную гладкость поверхности. Антистатическая технология используется для снятия статического электричества, которое способствует быстрой нагрузке и избыточной шлифовальной пыли, тем самым увеличивая срок службы ремня.
Отделка
- 5 В зависимости от конечного продукта панели могут подвергаться различным этапам отделки.Возможно нанесение различных цветов лака, а также различных рисунков под дерево.
Гильотинная резка используется для резки древесноволокнистых плит на большие листы (например, шириной 100 дюймов). Для листов меньшего размера, таких как 42 на 49 дюймов (107 на 125 см), используется высечка. Специальные машины используются для резки ДВП на узкие полосы шириной от 1 до 24 дюймов (от 2,5 до 61 см).
- 6 Ламинаторы используются для нанесения на поверхность винила, фольги и других материалов. Этот процесс включает в себя разматывание рулона древесноволокнистого материала, его подачу между двумя валами, на которые наносится клей, объединение покрытой клеем древесноволокнистой плиты с ламинирующим материалом между другим набором валов и отправку объединенных материалов в ламинатор.
Контроль качества
Большинство заводов МДФ используют компьютеризированный контроль процесса для контроля каждого этапа производства и поддержания качества продукции. В сочетании с непрерывными грузовыми лентами, измерителями основного веса, мониторами профиля плотности и толщиномерами поддерживается однородность продукта. Кроме того, Американский национальный институт стандартов установил спецификации продукта для каждого применения, а также предельные значения выбросов формальдегида. Поскольку экологические нормы и рыночные условия продолжают меняться, эти стандарты пересматриваются.
Последний стандарт для MDF, ANSI Standard A208.2, является третьей версией этого отраслевого стандарта. Этот стандарт классифицирует МДФ по плотности и использованию (внутри или снаружи) и выделяет четыре сорта продукции для внутренней отделки. Определенные спецификации включают в себя физические и механические свойства, допуски на размеры и пределы эмиссии формальдегида. Спецификации представлены как в метрических, так и в дюймово-фунтовых пределах.
Измеряемые физические и механические свойства готового продукта включают плотность и удельный вес, твердость, модуль разрыва, сопротивление истиранию, ударную вязкость, модуль упругости и предел прочности при растяжении.Кроме того, также измеряются водопоглощение, набухание по толщине и прочность внутренней связи. Американское общество испытаний материалов разработало стандарт (D-1037) для проверки этих свойств.
Будущее
Хотя в 1996 году было построено более 750 новых заводов, в 1997 году ожидалось, что потребление МДФ упадет на 10% ниже прогнозируемого уровня. Показатели использования снизились для некоторых рынков, а экспорт сократился. Несмотря на эту тенденцию, некоторые заводы продолжат инвестировать в высокотехнологичное оборудование и экологический контроль для производства высококачественной продукции.
Экологические нормы будут по-прежнему бросать вызов промышленности древесноволокнистых плит. Хотя карбамидоформальдегидные смолы в основном используются в производстве МДФ из-за их низкой стоимости и характеристик быстрого отверждения, они имеют потенциальные проблемы с выделением формальдегида. Возможным решением являются фенолформальдегидные смолы, поскольку они не выделяют формальдегид после отверждения. Эти смолы, однако, более дорогие, но предварительные исследования показали, что их можно использовать в гораздо меньших количествах и добиться того же времени обработки, что и мочевинной смолы.
Будут продолжены разработки в области производственных технологий, включая оборудование для обработки панелей и режущие инструменты. Со временем будет разработано прессовочное оборудование, которое устранит предварительное отверждение и уменьшит разброс толщины отдельных панелей. МДФ и другие изделия из инженерной древесины станут еще более однородными по характеристикам кромок и гладкости поверхности, а также будут иметь лучшие физические свойства и постоянство толщины. Эти улучшения приведут к тому, что все больше производителей мебели и шкафов будут включать такие продукты в свои проекты.
Где узнать больше
Периодические издания
«Руководство для покупателей и спецификаторов ДСП и МДФ». Wood & Wood Products, , январь 1996 г., стр. 67-75.
Кениг, Карен. «Новый завод МДФ отличается высокими технологиями и качеством». Wood & Wood Products, , апрель 1996 г., стр. 68-74.
«Древесина Ласани — идеальная замена дереву». Economic Review, , апрель 1996 г. , с. 48.
Маргосян Рич. «Новые стандарты для ДСП и МДФ. Wood & Wood Products, January 1994, pp. 90-92.
Other
The Particle Board/Medium Density Fiberboard Institute. Laurel M. Sheppard
Что такое МДФ?
Древесноволокнистая плита средней плотности (МДФ) представляет собой конструкционный продукт из древесины, изготавливаемый путем расщепления остатков твердой или мягкой древесины на древесные волокна, часто в дефибраторе, смешивания их с воском и смоляным связующим и формирования панелей с применением высокой температуры и давления.МДФ обычно плотнее фанеры. Он состоит из отдельных волокон, но может использоваться в качестве строительного материала, аналогичного по применению фанере. Он прочнее и намного плотнее ДСП.
Существует несколько неправильных представлений о плитах МДФ, которые часто путают с фанерой и древесноволокнистыми плитами. Плита МДФ — это аббревиатура от древесноволокнистой плиты средней плотности. Он в основном считается заменителем древесины и завоевывает промышленность как полезный материал для декоративных изделий, а также домашней мебели.
Если вы не знакомы с древесиной МДФ, мы расскажем вам, что это такое, проблемы с древесиной МДФ, как изготавливаются плиты МДФ.
Материал МДФ был создан путем расщепления твердой и мягкой древесины на древесные волокна. МДФ обычно состоит из 82 % древесного волокна, 9 % карбамидоформальдегидного клея, 8 % воды и 1 % парафина. а плотность обычно составляет от 500 кг/м 3 (31 фунт/фут 3 ) до 1000 кг/м 3 (62 фунта/фут 3 ).Диапазон плотности и классификация как легкая , стандартная или высокая плотность плита является неправильным и запутанным. Плотность плиты, если ее оценивать по отношению к плотности волокна, из которого изготовлена панель, имеет важное значение. Толстая панель МДФ плотностью 700–720 кг/м 3 может считаться панелью высокой плотности в случае панелей из хвойного волокна, тогда как панель такой же плотности из волокна твердой древесины таковой не считается.
Сырье, из которого изготавливается МДФ, должно пройти определенный процесс, прежде чем оно станет пригодным.Большой магнит используется для удаления любых магнитных примесей, а материалы разделяются по размеру. Затем материалы сжимаются для удаления воды, а затем подаются в рафинер, который измельчает их на мелкие кусочки. Затем добавляется смола, чтобы помочь волокнам склеиться. Эта смесь помещается в очень большую сушилку, которая нагревается газом или маслом. Эта сухая смесь проходит через барабанный компрессор, оснащенный компьютеризированным управлением, чтобы гарантировать надлежащую плотность и прочность. Полученные куски затем обрезают до нужного размера с помощью промышленной пилы, пока они еще теплые.
Волокна обрабатываются как отдельные, но неповрежденные волокна и сосуды, изготавливаемые сухим способом. Затем щепа прессуется в небольшие пробки с помощью шнекового питателя, нагревается в течение 30–120 секунд для размягчения лигнина в древесине, а затем подается в дефибратор. Типичный дефибратор состоит из двух вращающихся в противоположных направлениях дисков с канавками на их поверхностях. Стружка подается в центр и подается наружу между дисками под действием центробежной силы. Уменьшающийся размер канавок постепенно разделяет волокна, чему способствует размягченный лигнин между ними.
Из дефибратора целлюлоза поступает в «выдувную линию», характерную часть процесса производства МДФ. Это расширяющийся кольцевой трубопровод, первоначально диаметром 40 мм, увеличивающийся до 1500 мм. На первом этапе впрыскивается воск, который покрывает волокна и равномерно распределяется за счет турбулентного движения волокон. Затем в качестве основного связующего вводят карбамидоформальдегидную смолу. Воск улучшает влагостойкость, а смола изначально помогает уменьшить комкование. Материал быстро высыхает в последней нагретой расширительной камере выдувной линии и расширяется в тонкое, пушистое и легкое волокно.Это волокно может быть использовано немедленно или сохранено.
Сухое волокно всасывается в верхнюю часть «пендистора», который равномерно распределяет волокно в виде однородного мата под ним, обычно толщиной 230–610 мм. Мат предварительно сжимается и либо сразу отправляется в горячий пресс непрерывного действия, либо разрезается на большие листы для горячего пресса с несколькими отверстиями. Горячий пресс активирует связующую смолу и устанавливает профиль прочности и плотности. Цикл прессования работает поэтапно, при этом толщина мата сначала сжимается примерно до 1.5-кратная толщина готовой плиты, затем поэтапно сжимается и выдерживается в течение короткого периода времени. Это дает профиль плиты с зонами повышенной плотности и, следовательно, механической прочности вблизи двух сторон плиты и менее плотной сердцевиной.
После прессования МДФ охлаждается в звездообразной сушилке или охлаждающей карусели, обрезается и шлифуется. В некоторых случаях плиты также ламинируют для дополнительной прочности.
Masonite, ДВП и плиты меньшей плотности на JSTOR
АбстрактныйАвтор обсуждает раннее использование в XIX и XX веках лигноцеллюлозных древесноволокнистых плит художниками.Определены и обсуждены древесноволокнистые плиты и плиты «мазонитского процесса», а также уточнены даты патентов, в том числе возможность того, что древесноволокнистые плиты были доступны художникам еще в 1861 году, судя по двум британским патентам той даты, и тот факт, что древесно-волокнистые плиты были серийно производился в Англии к 1893 году. Обсуждаются преимущества и недостатки масонита в качестве основы для рисования художника, а также новый оргалит типа масонита, который был недавно представлен.
Информация о журнале Журнал Американского института консервации (JAIC) — международное рецензируемое периодическое издание для специалистов по консервации произведений искусства.Журнал публикует статьи о тематических исследованиях лечения, текущих проблемах, исследованиях материалов и технических анализах, касающихся консервации и сохранения исторических и культурных произведений. Темы охватывают широкий спектр специальностей, включая архитектурные материалы, археологические объекты, книги и бумагу, этнографические материалы, предметы, картины, фотоматериалы, скульптуру и деревянные артефакты. Начавшись как Бюллетень Американской группы Международного института охраны природы (IIC-AG) в апреле 1961 года, журнал приобрел свой нынешний вид в 1977 году.С тех пор JAIC стал хранилищем основной информации о консервации благодаря документированию новых материалов, меняющихся методов и разработки стандартов в профессии консерватора. Четырехцветное издание распространяется три раза в год среди членов АИК, а также среди подписчиков музеев, библиотек и университетов.
Основываясь на двухсотлетнем опыте, Taylor & Francis за последние два десятилетия быстро выросла и стала ведущим международным научным издательством.Группа издает более 800 журналов и более 1800 новых книг каждый год, охватывающих широкий спектр предметных областей и включающих оттиски журналов Routledge, Carfax, Spon Press, Psychology Press, Martin Dunitz и Taylor & Francis. Taylor & Francis полностью предана своему делу. публикации и распространению научной информации самого высокого качества, и сегодня это остается первоочередной задачей.
%PDF-1.6
%
181 0 объект
>/Метаданные 178 0 R/AcroForm 182 0 R/Страницы 168 0 R/Тип/Каталог>>
эндообъект
178 0 объект
>поток
2006-09-20T15:50:36-04:00Acrobat Capture 3.02011-10-31T14:34:21-04:002011-10-31T14:34:21-04:00Adobe PDF Library 4.0application/pdfuuid:466bcb88-6f89-4e4c-a927-531ba5c6a716uuid:44d71e0e-d03c-4416 90b18f0e54c9 конечный поток
эндообъект
182 0 объект
>/Кодировка>>>>>
эндообъект
168 0 объект
>
эндообъект
169 0 объект
>
эндообъект
170 0 объект
>
эндообъект
171 0 объект
>
эндообъект
172 0 объект
>
эндообъект
173 0 объект
>
эндообъект
174 0 объект
>
эндообъект
175 0 объект
>
эндообъект
176 0 объект
>
эндообъект
177 0 объект
>
эндообъект
118 0 объект
>/Содержание 238 0 R/Повернуть 0/MediaBox[0 0 619. 919 801]/Ресурсы>/Шрифт>/ProcSet[/PDF/Text/ImageB]>>/Тип/Страница>>
эндообъект
121 0 объект
>/Contents 239 0 R/Rotate 0/MediaBox[0 0 610,56 795,599]/Resources>/Font>/ProcSet[/PDF/Text/ImageB]>>/Type/Page>>/Type/Page>>
эндообъект
124 0 объект
>/Contents 240 0 R/Rotate 0/MediaBox[0 0 617.039 800.64]/Resources>/Font>/ProcSet[/PDF/Text/ImageB]>>/Type/Page>>/Type/Page>>
эндообъект
127 0 объект
>/Contents 241 0 R/Rotate 0/MediaBox[0 0 619,199 799,56]/Resources>/Font>/ProcSet[/PDF/Text/ImageB]>>/Type/Page>>
эндообъект
130 0 объект
>/Содержание 242 0 R/Повернуть 0/MediaBox[0 0 613.8 798.119]/Ресурсы>/Шрифт>/ProcSet[/PDF/Текст/ИзображениеB]>>/Тип/Страница>>
эндообъект
133 0 объект
>/Contents 243 0 R/Rotate 0/MediaBox[0 0 625.679 806.039]/Resources>/Font>/ProcSet[/PDF/Text/ImageB]>>/Type/Page>>/Type/Page>>
эндообъект
136 0 объект
>/Contents 244 0 R/Rotate 0/MediaBox[0 0 623,519 804,599]/Resources>/Font>/ProcSet[/PDF/Text/ImageB]>>/Type/Page>>/Type/Page>>
эндообъект
139 0 объект
>/Contents 245 0 R/Rotate 0/MediaBox[0 0 622.
겲KXͻp)|3*k䮢5mb5_6RK[S*Ev-m=ϴ4u+B0fa /ְa*myZO.oR1N[uUb5acRp4\:eu,pNnEQ]Xp/oÄSCynBbR?ZJe1aspoke-#I\H _zpR=W}*e0+_2
HWi4-%̠i=BA))0HvL DJM)2_zj#b4
Снижение выделения формальдегида из древесноволокнистых плит средней плотности с помощью хитозана в качестве поглотителя генерируют аналогичное количество отходов MDF (wMDF) после срока службы более двадцати годы. Производство wMDF вызовет экологические проблемы при захоронении или сжигание, которое требует переработки wMDF в переработанный MDF (rMDF).Тем не менее переработка wMDF — непростая задача, поскольку они содержат мочевиноформальдегид (UF) смолы в качестве клея для соединения волокон. Поэтому данная диссертация посвящена развитию клеевые технологии для переработки wMDF в панель rMDF. Эта диссертация состоит из девяти глав, в которых обсуждаются адгезивные технологии для переработка wMDF. Вкратце, в первой главе представлено общее введение в данное исследование. включая предысторию, цели и организацию диссертации. Вторая глава проанализировали доступную литературу по МДФ, УФ-смолам, окисленному крахмалу (ОС) и переработка wMDF.

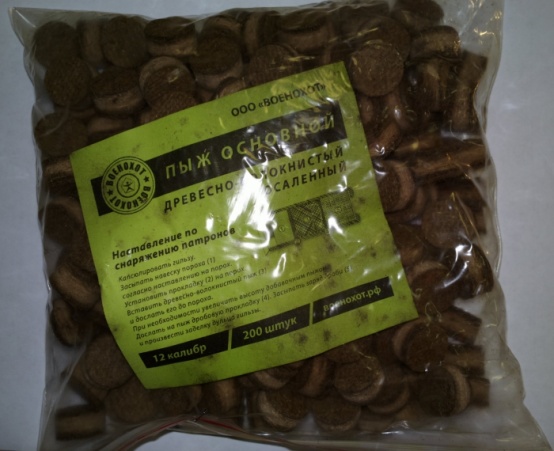


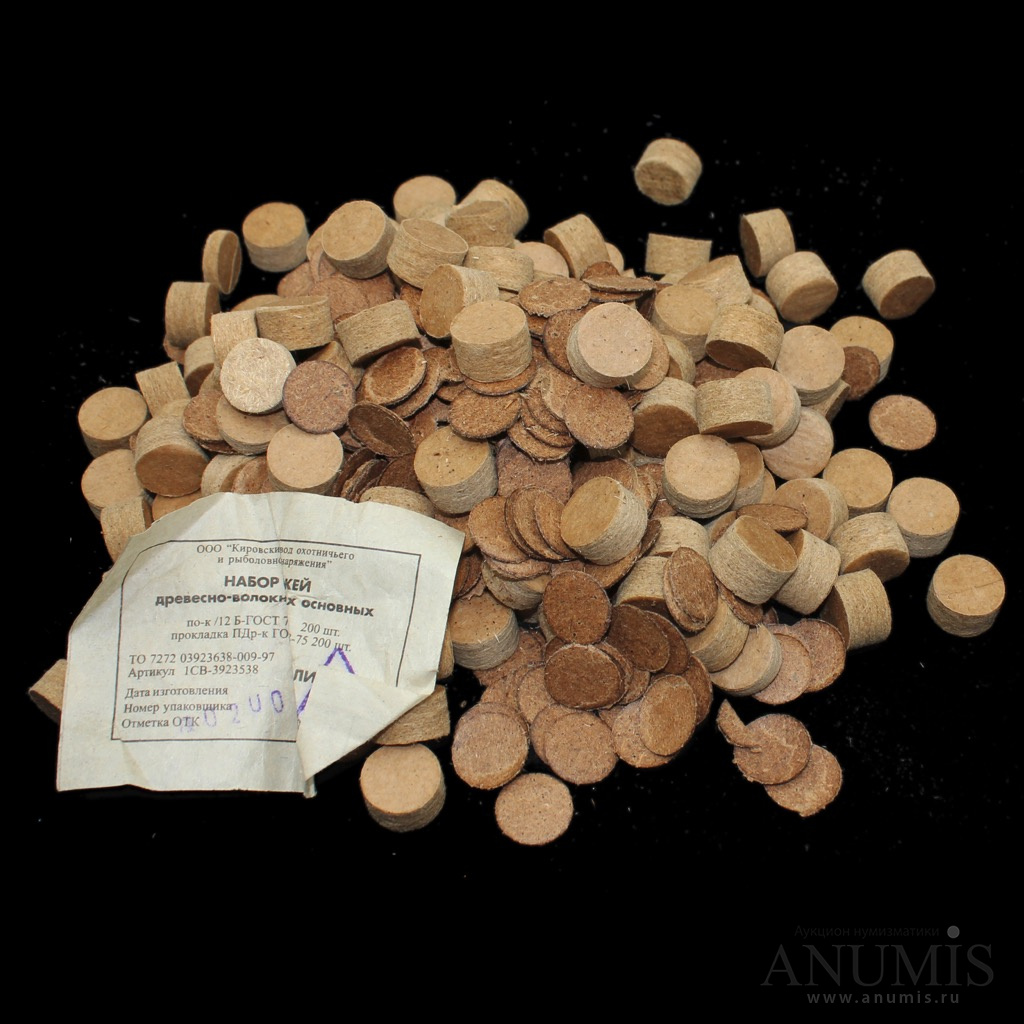
Шкаф превратился в грязную комнату, часть. 1 • ОЧЕНЬ ПОЗДНО
Всем привет, последние несколько недель мы работали как сумасшедшие. Думаю, Новый год пробуждает во мне организованность и мотивацию! У меня так много проектов, которые я хочу сделать дома, и пару выходных назад у нас были свободные выходные, поэтому по прихоти мы начали с нашего шкафа, который превратился в прихожую. Мы живем в двухуровневом доме, поэтому, когда мы заходим в дверь, у нас есть небольшой шкаф для верхней одежды и лестница, ведущая наверх или вниз.Почему-то моя семья, и я в том числе, просто не могут повесить пальто. Это что-то о том, чтобы открыть дверь, взять вешалку, повесить ее и положить обратно, с чем мы не можем справиться. Мне всегда нравился внешний вид прихожей, поэтому мы решили сделать мини-прихожую в нашем гардеробе. Вот как шкаф выглядел раньше:
Для начала мы сняли двери и подготовили стены к покраске. Так как это был шкаф для верхней одежды, по краям было несколько отверстий от дверных винтов и зазубрин.Дверь нанесла некоторый ущерб помещению. Мы использовали Dry Dex, чтобы заполнить дыры и царапины.
Мы дали ему высохнуть на ночь, так как некоторые участки Dry Dex были довольно тяжелыми и толстыми. На следующее утро мой муж отшлифовал участки, и пришло время перевесить полку. Предыдущая полка была из ДВП и выглядела совсем некрасиво. Мы предложили это, и я хотел, чтобы полка была немного выше, поэтому мы купили 2 × 4 и обрезали ее по размеру. Мы ставим по две с каждой стороны шкафа, чтобы держать нашу новую полку.В качестве полки мы использовали доску размером 10×8, чтобы она соответствовала длине шкафа. Я использовал один из моих любимых красителей, Weathered Grey.
Предыдущие полочные доски снимать побоялись, так как гипсокартон выдирать не хотелось. Мы решили оставить их там, убрать крючки и добавить еще одну доску к задней части шкафа, чтобы сделать его более цельным. Я хотел, чтобы здесь висели пальто, поэтому я сделал так, будто это должно было быть там специально!
Затем мой муж зашпаклевал некоторые места между деревяшками, чтобы они выглядели чистыми и не имели линий или открытых краев на деревяшках.
Когда герметик высох (в инструкции указано время высыхания 2 часа), пришло время красить! Это было то, что я был действительно взволнован, чтобы сделать. Я хотел покрасить доски для вешалок в белый цвет, чтобы они выделялись и выделялись белым цветом на ярком синем фоне, который я выбрал для стены. Я действительно хотел сильный цвет, который произведет впечатление, когда вы войдете в дом. Я пошел с Naval Шервином Уильямсом. Я влюблена в этот цвет и мне нравится, как он выглядит. Это очень темный цвет, поэтому потребовалось два слоя краски, чтобы получить хороший полный слой краски. Ниже один слой темно-синего цвета.
Сначала я покрасил в синий цвет и обклеил доску моей любимой лентой Frog, прежде чем покрасить доску. Когда вся краска высохнет, бело-голубая, пришло время повесить плечики. Измеряли так, чтобы они висели ровно. Мы сделали 4 на задней стенке и по 2 на каждой стороне. Это дает нам возможность повесить несколько пальто, когда к нам приходят гости.
Шкаф прошел долгий путь, но эта обувь, лежащая на коврике внизу шкафа, просто не подходит! 🙂 Наш план состоит в том, чтобы построить кабину для обуви в нижней части прихожей со скамейкой наверху.Мы хотим, чтобы наша дочь и будущие дети сидели там и надевали свое снежное снаряжение, прежде чем выйти на улицу и поиграть!
Я очень доволен тем, как все получилось, и с нетерпением жду возможности построить домик. Оставайтесь с нами, чтобы узнать, как это сделать и окончательно раскрыть! Желаю всем отличных выходных! Начну красить кухонные шкафы! Я не могу дождаться, чтобы преобразовать еще одно пространство в нашем доме! Кто-нибудь еще получает кайф от DIY?!
Многие исходящие ссылки на Refashionably Late являются партнерскими ссылками.